Cooling of Transformer: Best Methods Explained
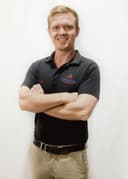
Keagan Arthur
2/26/2025

The cooling of transformer process is essential to prevent overheating and ensure efficient operation. This article covers different methods for cooling transformers, their applications, and benefits. By the end, you’ll know how to choose the right cooling method for any transformer.
Key Takeaways
- Understanding transformer cooling classes is essential for optimizing performance, safety, and lifespan while preventing overheating.
- Different cooling methods, such as ONAN, ONAF, and OFAF for oil-immersed transformers, and natural or forced air for dry-type transformers, address varying cooling needs based on transformer size and load requirements.
- Choosing the appropriate cooling method impacts transformer performance, efficiency, and maintenance costs, making it critical to consider factors like load capacity and environmental conditions.
Understanding Transformer Cooling Classes
Cooling classes form the basis of transformer cooling methods, specifying how efficiently heat is dissipated from the core and windings. For those involved in transformer design, maintenance, or operation, grasping these classes is essential. These classes guide decisions that enhance transformer performance, safety, and lifespan.
Each class indicates specific cooling methods and efficiencies. Liquid-filled transformers use oil or synthetic insulating liquids for cooling and insulation. Common classes include ONAN, ONAF, and OFAF.
These classes ensure transformers run efficiently without overheating, preventing insulation failure and extending their life. Forced air circulation is often employed to enhance cooling efficiency, especially in medium-capacity transformers where passive systems might fall short.
Importance of Cooling Classes
Cooling classes greatly influence design parameters like size, installation requirements, and maintenance costs. An effective cooling system can make a transformer more compact and economical. The chosen cooling method also impacts efficiency by managing winding temperature and reducing energy losses in transformer cooling systems.
Prolonged high temperatures can reduce transformer efficiency, making the choice of an appropriate cooling class crucial for reliable operation. Effective cooling strategies optimize performance and prevent costly downtime.
Oil-Immersed Transformer Cooling Methods

Oil-immersed transformers are vital components of the electrical grid, known for their excellent insulation and ability to handle high power densities. Their performance and efficiency are largely determined by the chosen cooling method. Advanced systems, such as the oil forced water method, use forced oil circulation with water-cooled heat exchangers to dissipate heat effectively in high-power applications.
The image displays a two-dimensional temperature distribution that reveals a critical hot spot at the low-voltage winding, where temperatures reach approximately 376.4 K. This finding emphasizes the increased risk of transformer failure due to prolonged exposure to high temperatures, particularly under extreme climatic conditions.
Consequently, various cooling methods, including ONAN, ONAF, and OFAF have been developed to address these challenges and ensure optimal transformer performance.
ONAN Cooling System
The ONAN (Oil Natural Air Natural) system is a passive method that relies on natural convection for heat dissipation, making it suitable for smaller transformers where surrounding air naturally circulates.
This method uses mineral oil that circulates naturally within the tank, transferring heat to the outer surfaces. The ONAN system is cost-effective and easy to maintain, providing sufficient cooling for smaller applications.
ONAF Cooling System
The ONAF (Oil Natural Air Forced) system enhances natural convection by using fans to blow air over the heat exchangers, allowing the transformer to handle higher loads up to about 60 MVA.
Forced air over the cooling fins improves heat transfer, increasing the transformer’s capacity from 2500 kVA to 3125 kVA. This method suits transformers needing more cooling than natural convection provides.
OFAF Cooling System
The OFAF (Oil Forced Air Forced) method integrates forced oil circulation and forced air cooling, designed for larger transformers where natural convection is insufficient.
In the OFAF system, oil is pumped through heat exchangers, with air forced over these exchangers to dissipate heat. This dual approach ensures uniform temperature distribution, enhancing performance and reliability.
Dry-Type Transformer Cooling Methods

Dry-type transformers use air or dry mediums for cooling, unlike oil-immersed types. They rely on ambient air to circulate around the windings and core, effectively dissipating heat. Primary cooling mechanisms include natural air convection and forced air cooling, each serving specific needs based on transformer size and load requirements.
In the image above, we observe the temperature distribution within a conventional oil-immersed transformer. The symmetrical temperature contour shows a gradual temperature reduction from the top to the bottom of the heat sink, with the sides slightly cooler than the central heat sink. This phenomenon is due to convective heat exchange, where the transformer oil flows in a certain direction, absorbing heat.
As the oil’s temperature rises, its density decreases, and buoyancy causes the fluid to move. The cooling process repeats cyclically, facilitating efficient heat exchange within the transformer. For dry-type transformers, natural air convection is a passive method where cooler air is absorbed and circulated without mechanical assistance, handling transformers in cooler climates or smaller sizes effectively.
Forced air cooling, on the other hand, leverages fans or blowers to actively circulate air over transformer components, making it ideal for high-load or confined environments. Each method is critical for maintaining proper functioning and preventing overheating in dry-type transformers, ensuring reliable performance and longevity in various usage conditions.
Temperature Distribution in Conventional Oil-Immersed Transformers
The above image shows the temperature distribution contours of a conventional oil-immersed transformer. The distribution is symmetrical within the enclosure, with temperatures gradually decreasing from top to bottom. The heat sinks in the middle register slightly higher temperatures than those on the sides, influenced by convective heat exchange with the surrounding air.
As hot oil flows upward due to buoyancy, it transfers heat through the collecting pipe and tank walls, then settles back down to reabsorb heat from the core and windings. This cyclical flow pattern ensures continuous heat removal from the active parts of the transformer.
Dry-Type Transformer Cooling Methods
Dry-type transformers use air or dry mediums for cooling, distinct from oil-immersed types. They rely on ambient air to circulate around the windings and core, dissipating heat. Primary cooling mechanisms in dry-type transformers include natural air convection and forced air cooling, each tailored to specific needs.
Natural Air Convection
Natural air convection is a passive method for dry-type transformers, relying on surrounding air to absorb heat without mechanical assistance. The heat generates convection currents, facilitating airflow around the coils and promoting natural air cooling. Vents in the enclosure allow cooler air to circulate naturally, absorbing and dissipating heat. This simple, cost-effective method suits smaller transformers or those in cooler climates.
Forced Air Cooling Systems
Forced air cooling systems use fans or blowers to enhance heat dissipation, making them suitable for higher load applications. By forcing air over transformer components, they quickly disperse heat, ensuring a more controlled and efficient cooling process. This method is ideal for transformers in confined spaces or higher temperature environments, where natural air convection is insufficient. Forced air cooling helps maintain optimal temperatures, promoting reliable performance and extending transformer life.
Internal and External Cooling Media

The above image provides a schematic view of the transformer’s main components, including the internal heat source, high- and low-voltage windings, silicon steel core, transformer oil domain, external casing, and chip heat sink. These elements are arranged around the transformer’s geometric center and form the basis for analyzing the impact of raised structures on heat flow.
Understanding how these internal and external parts interact is key to selecting effective cooling media. Internal media, such as mineral oil, serve both as coolants and insulators, while external media, including ambient air or water-cooled surfaces, facilitate heat dissipation.
Internal Cooling Mediums
Internal cooling mediums like mineral oil and natural esters absorb and dissipate heat while providing electrical insulation, enhancing reliability and performance.
KNAN and KNAF transformers use natural esters for internal cooling, leveraging natural convection to circulate the medium and dissipate heat. Chosen for thermal stability and reduced flammability, these fluids suit various applications.
External Cooling Mediums
External cooling mediums like ambient air and water-cooled surfaces dissipate heat into the environment. For KNAN and KNAF transformers, air is the primary medium, utilizing natural or forced convection.
Oil forced water systems are an advanced cooling method for high-capacity transformers, where forced oil circulation works in tandem with water-cooled heat exchangers to effectively dissipate heat.
Water-cooled surfaces often pair with heat exchangers to optimize cooling. These methods ensure efficient operation and optimal temperatures, even in demanding conditions.
Factors Influencing Cooling Method Choice
Several factors influence cooling method choice, including load capacity, environmental conditions, and operational requirements. Higher loads require more efficient methods like OFAF, OFWF, or forced air circulation to handle additional heat.
Conditions like hot ambient temperatures impact cooling method choice. Hotter areas need robust cooling to prevent increased losses and ensure reliability. Cooling methods must adapt to these factors to maintain efficiency and longevity.
Impact of Cooling Methods on Transformer Performance
Selecting the right cooling method significantly impacts performance, efficiency, and maintenance costs. Effective systems protect transformers from thermal damage, enhancing kVA capacity and ensuring reliable power distribution.
Oil-immersed transformers operate efficiently under high loads due to effective heat transfer. Cooling method choice also depends on factors like humidity and altitude. Proper strategies improve reliability, reduce maintenance, and ensure long-term efficiency.
Synkhem Petrochemicals' Role in Transformer Cooling
Synkhem Petrochemicals, South Africa’s leading supplier of base and transformer oils, plays a pivotal role in cooling. They offer high-quality oils like T 1500 GPN and T1500Y-NRC to enhance transformer performance and reliability.
Direct partnerships with leading refineries ensure the purity and performance of Synkhem’s oils, which undergo rigorous testing through three independent labs to meet industry standards. This commitment to quality makes Synkhem a trusted industry partner.
credit: Bingshan Ma, Runxin Hu, Ye Wang, Yang Cheng | A study on the optimization of cooling performance for oil-immersed transformers in high temperature environments utilizing response surface methodology
Beyond high-quality products, Synkhem offers multiple purchasing options, providing flexibility, efficiency, and cost savings. Their innovative ‘Ship on Water’ option minimizes handling costs and reduces contamination risk. Synkhem’s solutions ensure efficient, reliable transformer operation.
Get in Touch for Transformer Oil
Comments
No comments yet. Be the first to comment!
You must be logged in to comment.