What Makes Group I Base Oil and Group II Different?
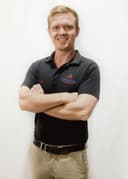
Keagan Arthur
6/26/2025

What You Don’t Know About Your Base Oil Could Be Costing You Millions
In industries where downtime costs thousands per hour, the type of base oil you use is a strategic asset.
Yet, across South Africa and much of the continent, many operations still rely on Group I base oils because they’ve always worked. The challenge now? Global production of Group I is shrinking fast. Major international refiners are pulling out. Supply is tightening and procurement teams across Africa are left exposed, often without realizing it.
At the same time, Group II base oils are longer-lasting, cleaner-burning, and increasingly specified by OEMs and global partners, becoming the new global standard. For some operations, making the switch is a clear upgrade. For others, especially those running legacy equipment, Group I industrial oils may still be the right fit if you can secure the right formulation and quality.
Based on your equipment, your sector, and your goals, we will help you choose the solution that protects your uptime, sharpens your compliance, and strengthens your long-term ROI.
Ten minutes now could save hundreds of hours, and millions of rands, over the next 12 months.
Group I Base Oils: Where It Started
API Definition of Group I Base Oil
Group I base oils are defined by the American Petroleum Institute (API) as containing:
- Less than 90% saturated hydrocarbons
- More than 0.03% sulfur
- A viscosity index (VI) between 80 and 120
These industrial oils are mineral-based and were considered the most traditionally refined category in the base oil spectrum. They served as the industry standard for decades before newer refining technologies became mainstream.
Refining Method and Physical Characteristics
Group I oils are produced using a method called solvent refining, where chemical solvents are used to separate lubricant-grade molecules from crude oil. While efficient, this method leaves behind impurities such as sulfur compounds and aromatic hydrocarbons, which contribute to oil degradation over time.
This less advanced process results in a more chemically diverse molecular structure, making the oil less thermally stable and more prone to oxidation and sludge formation. A typical Group I oil has a brownish or amber hue due to these residual compounds and carries a stronger, more aromatic smell than its Group II counterpart.
The Global Shift Away from Group I Oils

Over the last two decades, the global lubricant industry has moved away from Group I oils in favor of Group II base stock, which is refined through hydrocracking and hydrotreating. These modern processes produce a clearer color, more stable oils with lower sulfur and better oxidation resistance, making them more suitable for high-performance applications and compliant with strict environmental standards.
In response, major refiners such as ExxonMobil, Shell, Eni, TotalEnergies, and Galp have shut down or repurposed their Group I refining units across the U.S., Europe, and Asia. As of 2011, Group I oils made up 57% of global base oil production; by 2019, that number had dropped to 37%, and is projected to fall below 30% by 2030.
Why Group I products Still Matters in Africa, and Especially in South Africa

Despite global trends, Group I remains widely used in South Africa and across much of the African continent. The reason is not performance, it’s cost, accessibility, and equipment compatibility.
Much of the machinery in use is decades old and was originally designed around Group I oil formulations. Retrofitting or upgrading this equipment to meet newer lubricant standards can be prohibitively expensive, particularly in cost-sensitive environments. For many business owners, Group I oils are still the most viable option to keep their operations running.
However, this reliance is becoming more complex. Companies like BP, Shell, and Engen have begun divesting or mothballing Group I production assets in South Africa, tightening local supply. As domestic refining declines, imports may become more expensive, forcing smaller businesses to reassess availability, pricing, and long-term product strategy.
The Practical Reality: Group I Still Gets the Job Done
While Group I is the least refined base oil, and does have limitations, such as shorter drain intervals, lower oxidation resistance, and higher environmental impact, they remain functional and dependable in the right context.
When used in applications that do not demand ultra-clean or ultra-stable oil, like older hydraulic systems, gearboxes, or compressors, Group I base oils continue to deliver reliable performance. With proper maintenance practices, including oil analysis and filtration, businesses can still run effectively using well-formulated Group I lubricants.
Group II Base Oils: Advancing Lubrication Technology
used in heavy duty engine oils and passenger car motor oils
API Definition of Group II Base Oils
According to the American Petroleum Institute (API), Group II base oils are characterized by:
- Saturates: ≥ 90%
- Sulfur Content: ≤ 0.03%
- Viscosity Index (VI): 80–120
These specifications indicate a higher degree of purity and stability compared to Group I oils, achieved through more advanced refining processes, resulting in the prolonged base oil life in high heat applications and extreme cold conditions.
Refining Process and Physical Characteristics
Group II base oils are produced using two advanced processes: hydrocracking and hydrotreating. These methods represent a major evolution in lubricant technology, delivering higher purity, chemical stability, and environmental alignment compared to earlier refining techniques.
Hydrocracking is a catalytic process that applies high temperature and pressure in the presence of hydrogen to break down large, unstable hydrocarbon chains into smaller, more stable ones. This not only improves molecular uniformity, but also increases the base oil’s viscosity index, thermal resistance, and longevity.
Hydrotreating complements this by removing unwanted elements, especially sulfur, nitrogen, and aromatic compounds, that are known to accelerate oil degradation and increase environmental and health risks. The result is a clear, colorless, low-odor base oil with significantly enhanced oxidation stability, superior resistance to thermal stress, and a dramatically lower sulfur footprint.
Key Performance Advantages of Group II Base Oils


The Environmental Trade-Off: What the Price Tag Doesn’t Tell You

When choosing between Group I and Group II base oils, it’s tempting to focus on the upfront price per Litre. But for industrial operators, the real cost is environmental, measured in emissions, waste volumes, disposal risks, and compliance burdens. While Group I oils remain more accessible in South Africa due to legacy equipment and procurement habits, they carry heavier environmental consequences that often go unaccounted for in purchasing decisions.
Waste Management: Volume, Classification, and Cost
Group I also creates more used oil waste over the product’s life cycle. Because they degrade faster, especially under heat, pressure, and load, they must be drained and replaced more frequently. This not only increases lubricant consumption, but also generates more hazardous waste volume that must be classified, stored, transported, and treated under South African waste regulations.
Under the National Environmental Management: Waste Act (NEM:WA), waste oil with high sulfur, metal, or sludge content may be classified under a higher hazard rating, triggering stricter storage, reporting, and disposal requirements. Group I oils are more likely to reach this threshold due to their solvent-refined impurities. This raises the administrative and financial burden on facility managers, particularly in sectors like mining and construction where oil volume is high and disposal options are limited.
By contrast, Group II oils allow for longer drain intervals and produce cleaner used oil, simplifying storage logistics and reducing the frequency and cost of hazardous waste removal.
Cost Consideration: Immediate vs Total Ownership

At first glance, Group I base oils appear more affordable. Per litre, they’re often cheaper than Group II, and for cost-sensitive sectors, that’s a compelling draw. But when you zoom out and look beyond procurement price to what it actually costs to run, maintain, and dispose of oil over a full year of operation, Group II frequently comes out ahead.
Let’s break down the true cost of lubrication by comparing operational variables between Group I and Group II over a two-year period. Below are the core categories where costs diverge:

While Group I may cost 15–20% less per litre, that savings is rapidly erased by increased downtime, shorter service intervals, and waste oil disposal costs. For equipment that operates year-round under high thermal or mechanical load, such as compressors, diesel fleets, or industrial gearboxes, the cumulative effect of shorter oil life compounds into significantly higher operational expenditure. This scales accordingly amongst the group iii base oils, up to group iv base oils which are completely synthetic base oils instead of mineral based.
Conclusion : Strategic Recommendations for South African Industry
For many South African industries, mining, construction, manufacturing, and transport, the upfront price of oil can feel like the deciding factor. While Group I base oils still offer a viable short-term solution, especially for older machinery, the long-term outlook is shifting rapidly.
Multinational suppliers like Shell, BP, and Engen are pulling back from Group I refining. Global regulatory pressures are tightening and domestic waste management laws are becoming more stringent. In this context, the price gap between Group I and Group II base oils is no longer the full story. It’s shrinking, and the operational risks of sticking with Group I are growing.
Group II base oils present a practical, forward-thinking choice. They reduce maintenance frequency, extend equipment life, and lower your environmental and regulatory risk profile. But for businesses running older models of machinery, or those navigating tight margins, there is still a place for high-quality Group I oils, provided they are formulated and supplied to modern performance standards.
That’s where Synkhem comes in. We provide for both base oil products. Consistently, and without interruption, so that your business is never forced to choose between performance and practicality.
Comments
No comments yet. Be the first to comment!
You must be logged in to comment.