What South African Giants Need to Know About Group II Base Oils
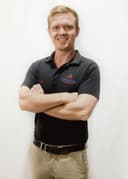
Keagan Arthur
6/27/2025

I'm not here to waste your time. You want to outperform your competitors, and boost your bottom line. I want that too. If you are a player in one of these key industries:
- Mining
- Road Freight (Logistics)
- Manufacturing
- Power Generation
- Or any operation that relies on Group I or Group II base oils
Take 10 minutes to read this, you could save yourself millions, because there’s a distinction you need to know.
We know that group I base oils are being phased out globally, and South Africa is starting to catch up. Across these industries, the shift to group II is underway, sold on the promise of cleaner specs and better performance.
However, group II base oil is a broad category definition.
There’s a wide range of quality within it, and the wrong oil will break your machinery, kill your uptime, and you won’t trace the failure back to the oil until it’s too late.
South Africa’s Unique Operational Demands

Here is a table with the API classifications for the 5 base oils:
Group II base oils are hydrocracked, meaning they undergo high-pressure hydrogen treatment to remove impurities. Oils from different suppliers can vary dramatically in thermal stability, volatility, cleanliness, and oxidative resistance - even though they all carry the same Group II label.
These differences are driven by how the oil was refined (mild vs severe hydrocracking), the origin of the crude oil (naphthenic vs paraffinic), and the effectiveness of the dewaxing and finishing processes. Some Group II base oils hold up under load, heat, and long drain intervals. Others degrade quickly by oxidising, shearing down in viscosity, or forming sludge and varnish.
This Matters More In South Africa

- In the Northern Cape mining belt, including Kolomela, Sishen, and Black Rock, machinery operates in open-pit sites where summer surface temperatures exceed 45°C. Equipment is exposed to fine dust, extreme load cycles, and round-the-clock operation, often with delayed services due to remote locations.
- In Gauteng and Durban’s long-haul freight corridors, trucks run overloaded on the N3 and N1, crossing steep grades in hot weather with inconsistent diesel quality. Oil drain intervals are frequently extended to cut costs, while high soot loading and thermal stress push lubricants to their limits.
- In eThekwini and Nelson Mandela Bay industrial zones, manufacturers deal with power surges, variable process loads, and old plant machinery. Oils face thermal shock, micro-contamination, and startup oxidation due to stop-start batch production.
- In Eskom’s regional power stations, such as Medupi and Arnot, generator turbines and engine sets are cycled intensively during load-shedding. These units operate under full load without stable cooldown phases, creating sustained heat zones that break down weaker base oils, especially in peaker plants or backup units that weren’t designed for daily cycling.
In settings like this all around South Africa, a technically compliant but chemically unstable Group II oil will degrade. Once it does, the failure shows up as varnish, stuck valves, heat soak, mechanical fatigue, and eventually, breakdown.
How to Identify a High-Quality Base Oil Groups

Here’s how to evaluate the actual quality of a Group II base oil before it ends up in your machines:
1. Viscosity Index (VI)
The Viscosity Index measures how stable the oil’s viscosity remains across temperature changes.
Group II base oils must meet a minimum VI of 80, but higher VI, typically 95 or above, indicates better thermal stability and film strength under stress. Look for a VI of 95 or higher to ensure reliable protection.
Higher VI oils maintain film strength during hot operating conditions - crucial for overloaded haulage trucks on the N3 between Johannesburg and Durban or crushers at Kolomela where thermal load is extreme. Oils with VI near 80 (the minimum for Group II) shear down quickly, losing protection when it’s needed most.
2. NOACK Volatility
This test indicates how much of the oil evaporates at high temperatures.
Look for a NOACK value under 10% - the lower, the better.
In hot zones like the Northern Cape or engine bays during load-shedding at Arnot power station, volatile oils thin out and disappear. This increases top-up costs and accelerates wear.
3. Oxidation Stability (TOST Life)
Measured using the ASTM D943 test, this simulates long-term thermal and oxidative stress.
Look for base oils with TOST values exceeding 5,000–7,000 hours.
Low-stability oils form acids and sludge faster, especially under load-cycling conditions like those in generator sets. The result is fouled internals, higher varnish risk, and seal degradation.
4. Base Number (TBN) and Retention Curve
The Total Base Number tells you how long the oil can neutralise acids before it fails.
Look for a strong starting TBN (typically 10–12 for diesel applications) and a slow drop-off over time.
In long-haul freight or standby power applications with extended drain intervals, poor TBN retention leads to corrosion, sludge, and rising TAN (acid number).
5. Feedstock Origin and Consistency
The crude source (paraffinic vs naphthenic) and how it’s processed determines molecular stability.
Ask if the oil is produced from a consistent, paraffinic feedstock. Was it severely hydrocracked or only mildly treated?
Inconsistent feedstock leads to unstable oil chemistry. Over time, this causes variable performance, shortened oil life, and higher deposit formation under identical operating conditions.
6. Color and Appearance (Secondary Check)
While not a primary performance metric, color can still reveal formulation problems.
Watch out for cloudiness, inconsistency between batches, or darker-than-expected oils.
Poorly refined or blended oils may indicate cost-cutting or lack of process control, both of which become evident after deployment.
Conclusion: What You Need to Know Now
Most stop at the spec sheet.
We don’t.
That’s how you stay ahead.
Comments
No comments yet. Be the first to comment!
You must be logged in to comment.